Manufacturing and inspection techniques for full welded ball valves
The full welded ball valve described in this article uses single spherical welding with a fully automatic welding process. The ball valve has characteristics of uniform force, reliable sealing, compact structure, light weight and high strength. It is a technical and economical pipeline ball valve, which is widely used at home and abroad.
Structure design of full welded ball valves
The structure of the full welded ball valve described herein is shown in the picture below. The biggest difference between this type of ball valve and the traditional three-way ball valve is that the way of full welded ball valve closing the ball is welded. Therefore, the inner and outer linings are important during the welding process. In addition, the installation of the ball valve on the pipeline is also by means of a welded connection.
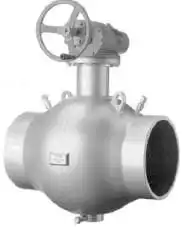
The seat sealing construction is generally double sealing (upstream and downstream double sealing). The valve seat inserts have excellent corrosion resistance, wear resistance and good elasticity, and high sealing performance. The structure of the valve seat is shown in the photo below.
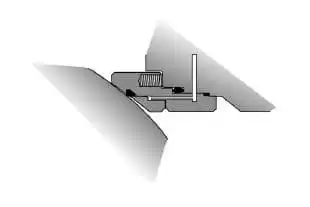
The principle of the valve seat double sealing construction is as follows
(1)Sealing principle of the upstream seat: Due to the upstream force, the seat is pressed by the ball to form a seal, as shown in Figure 3.
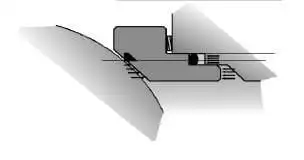
Sealing principle of the seat on the downstream side: The seat is sealed by the ball due to the pressure in the valve body, as shown in Figure 4.
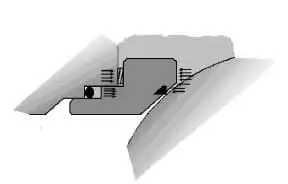