Precautions for welding of stainless steel pipe and pipe fitting
1. The power supply with vertical external characteristics is used, and the positive polarity is used when DC (welding wire is connected to the negative electrode).
2. Generally suitable for the welding of thin plates with a thickness of less than 6mm. It has the characteristics of beautiful welding seam and small welding deformation.
3. The protective gas is argon with a purity of 99.99%. When the welding current is 50 - 50A, the argon flow rate is 8 - 0L/min, and when the current is 50 - 250A, the argon flow rate is 2 - 5L/min.
4. The length of the tungsten electrode protruding from the gas nozzle is preferably 4 - 5mm. It is 2 - 3mm in the place with poor shielding such as fillet welding, and 5 - 6mm in the deep slot. The distance between the nozzle and the working is generally not more than 5mm.
5. In order to prevent the appearance of welding pores, the welding parts must be cleaned up if there is rust or oil stains.
6. When welding ordinary steel, the welding arc length is preferably 2 - 4mm, while when welding stainless steel, the welding arc length is preferably - 3mm. If too long, the protection effect is not good.
7. When bottom butt jointing, in order to prevent the back surface of the bottom bead from being oxidized, gas protection is also required on the back.
8. In order to make argon gas well protect the welding pool and facilitate the welding operation, the center line of the tungsten electrode and the workpiece at the welding place should generally maintain an angle of 80 - 85°, and the angle between the filler wire and the surface of the workpiece should be as small as possible, generally around 0°.
9. Windproof and ventilation. In windy places, please take measures for windshield, and take appropriate ventilation measures indoors.
(1) It is necessary to control the size of the groove of the joint of the stainless steel pipe and pipe fittings, thoroughly clean the welding root, and select the appropriate welding current and welding speed. For example, the butt joint formed by single-sided welding and double-sided forming, the gap between the pair should generally be equal to the diameter of the electrode, and the height of the blunt edge is about 1/2 of the diameter of the electrode.
(2) In the welding quality standard of stainless steel pipe and pipe fittings, the double-sided welding or the single-sided welding with a backing plate is not allowed to have defect of under-penetration. For single-sided welding without a backing plate, the allowed defect of under-penetration is related to the importance of the weld bead. For important weld bead, single-side under-penetration is not allowed; the more important weld beads are allowed to have a depth of under-penetration not more than 10%-15% of the thickness of the base metal (depending on the grade of the weld bead), and not more than 2m. The length of under-penetration does not exceed the total length of slag inclusion allowed by the weld bead of the same grade; generally, the depth of under-penetration at the end of the weld bead should be less than 20% of the thickness of the base metal, and no more than 3mm, and the length should also be less than the total length of the allowed edge.
(3) In order to prevent the mixing of other slag inclusions, the dirt and oxidation slag on the base material groove of stainless steel pipe and pipe fittings and its nearby surface should be strictly cleaned, and the slag of the previous weld bead should be thoroughly cleaned.
(4) In order to fully float the slag of stainless steel pipe and pipe fittings, a moderate welding current should be selected to make the molten pool reach a certain temperature to prevent the weld metal from cooling too quickly.
(5) Master operation technologies and always keep the molten pool clearly visible and promote good separation of molten slag and molten iron.
(6) Use neutral flame for gas welding. And, use welding wire to pull the slag out of the molten pool during operation.
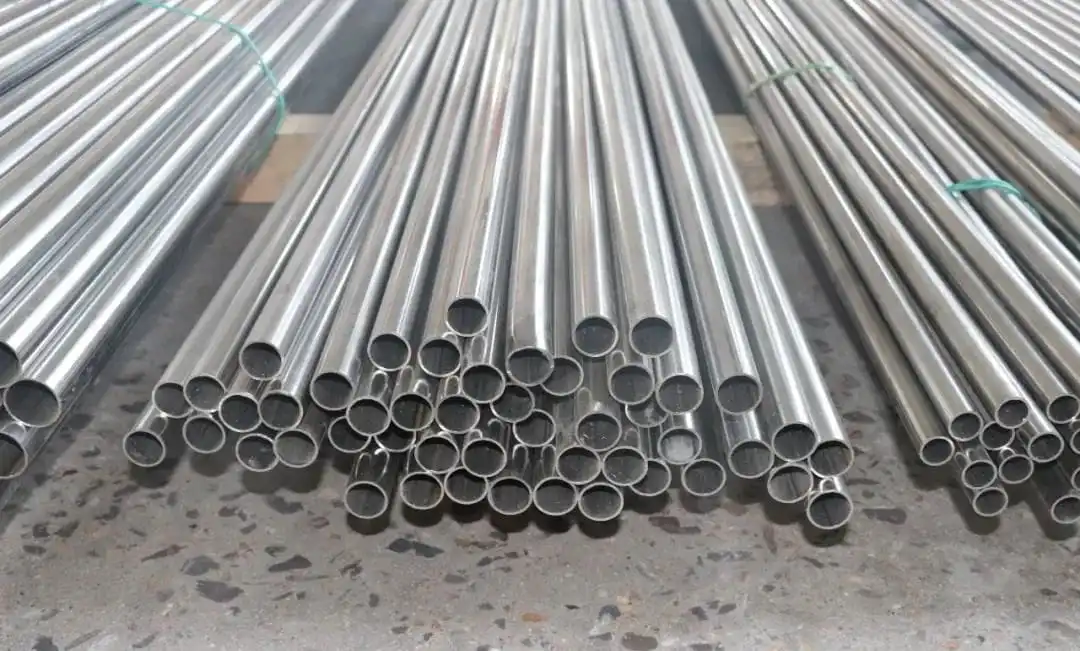